Case Studies | Global Food & Beverage Company
Reducing Detention Costs & Optimizing Yard Operations
A global food and beverage manufacturer partnered with ShipmentX to optimize yard operations, cut detention costs, and streamline billing across its supply chain.
33%
Detention Cost Reduction
100K+
Invoices Processed Annually
2x Faster
Invoice Reconciliation
20%
Lower Ops Overhead
The Client: Global Food & Beverage Manufacturer
A global leader in the snack and packaged foods industry, the client operates a vast logistics network supporting dozens of iconic consumer brands. With high shipment volumes and time-sensitive operations, efficiency and cost control are critical to their supply chain performance.
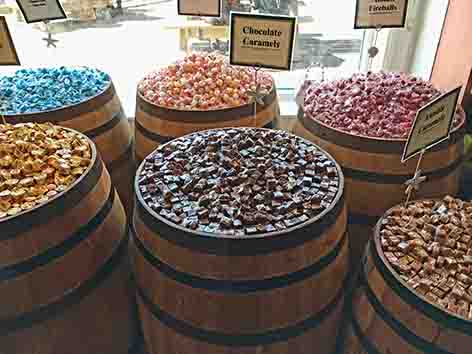
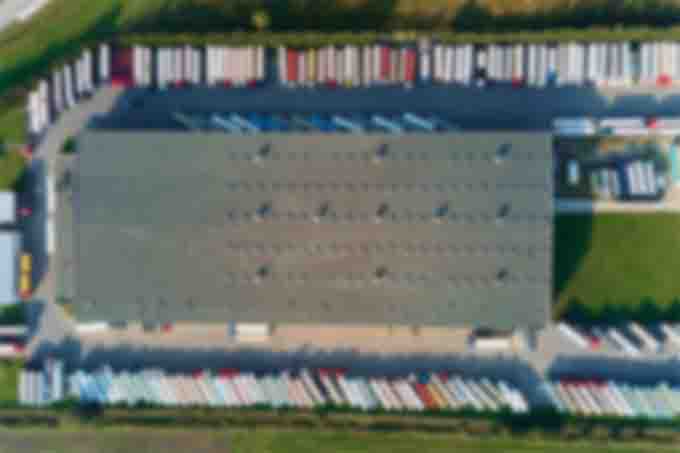
The Challenge
Despite having a strong logistics backbone, the client faced escalating detention charges and slow invoice processing due to inefficient yard operations and limited real-time coordination.
High Detention Charges
Delays in truck turnaround due to yard congestion led to increased detention costs.
Limited Yard Visibility
Lack of real-time tracking made it difficult to coordinate arrivals, docks, and resource allocation.
Slow Invoice Processing
Manual reconciliation created billing delays and strained vendor relationships.
The ShipmentX Solution
To reduce detention charges and optimize yard flow, ShipmentX implemented an integrated solution combining Yard Management, Dock Scheduling, WMS connectivity, and real-time GPS tracking.
Yard Management
Optimized gate-in/gate-out flow, truck movements, and dock assignments to reduce congestion and wait times.
Dock Scheduling
Enabled smoother coordination between transporters and warehouse teams to avoid overlapping or idle slots.
WMS Integration
Synchronized warehouse inventory updates with shipment movement to improve handling and reduce delays.
Telematics & GPS
Live vehicle tracking allowed for more accurate scheduling, visibility into delays, and improved yard planning.
Results & ROI
ShipmentX delivered measurable impact by reducing detention costs, improving visibility, and accelerating invoice processing—driving both soft gains and hard savings.
Reduced Yard Congestion
Improved scheduling and gate coordination minimized truck wait times.
Real-Time Visibility
Live GPS tracking enabled tighter control over inbound and outbound operations.
Faster Billing Cycles
Automated reconciliation improved invoice accuracy and reduced payment delays.
1/3 Detention Cost Reduction
Significant savings across 100,000 invoices annually through optimized yard flow.
Accelerated Invoice Processing
Shorter turnaround on freight data improved cash flow and vendor satisfaction.
Lower Operational Costs
Reduced manual workload and faster turnaround helped lower overhead.
What's Next
Building on early success, the client is scaling ShipmentX to more facilities while exploring AI-driven optimization and enhanced transporter performance tracking.
AI Yard Optimization
Using predictive analytics to forecast bottlenecks and dynamically optimize dock scheduling.
Carrier Performance Metrics
Measuring transporter KPIs to improve on-time rates, service consistency, and accountability.
Scalable Rollout
Extending ShipmentX solutions to more regional and global facilities to unify execution and insights.
Conclusion
By deploying ShipmentX's integrated Yard Management, Dock Scheduling, and Telematics solutions, the client significantly reduced detention charges and streamlined freight billing processes.
With measurable cost savings, improved visibility, and greater operational control, the company is well-positioned to expand ShipmentX across more sites—unlocking smarter, scalable, and more profitable logistics operations worldwide.
Drive Efficiency from First Mile to Final Delivery
Reduce costs. Move faster. Gain control. See how ShipmentX transforms supply chains for global leaders—and how it can for you.